Full oxygen combustion glass furnace design
Time:
Apr 02,2025
Design of an All-Oxygen Combustion Furnace
Many universities and design institutes in China have conducted theoretical research on all-oxygen combustion kilns. However, most all-oxygen combustion kilns in China are currently entirely imported, including design, technology, and even entire production lines. This not only leads to high investment but also slows down the development of our own all-oxygen combustion technology. In recent years, we have participated in the introduction and design transformation of several all-oxygen pool furnaces in China, conducted research on advanced foreign technologies, and accumulated some experience in the design of all-oxygen glass pool furnaces. Since the biggest difference between all-oxygen combustion kilns and regenerative kilns lies in the melting pool, this article only introduces the design of the melting pool.
2.1Kiln Pool
The design of the kiln pool in an all-oxygen combustion kiln is similar to that of a traditional air-combustion kiln. The most important aspect is determining the area and volume of the furnace.
First, based on the established furnace scale (daily output) and melting rate indicators, the melting pool area is estimated. At the same time, factors such as material preparation, clarification and homogenization, material properties and forming temperature, flame and combustion conditions should be considered comprehensively to select an appropriate length-width ratio. In the electronic glass industry, the length-width ratio is generally2~3. Second, after estimating the melting pool area, the area of the melting zone and the clarification zone can be theoretically calculated using the heat balance equation based on the melting process of the glass batch, to verify the estimated furnace area.
Due to the complex physical, chemical, and physicochemical reactions inside the furnace, some data, such as flow coefficient, flow layer thickness, and glass liquid temperature at various locations, have large errors. Theoretical calculations cannot fully reflect the complex situation inside the furnace, therefore, theoretical calculations should be combined with empirical values.
2.1.1Bottom Design of the Pool
The bottom design of the melting pool in an all-oxygen kiln is similar to that of an ordinary air-assisted kiln. According to the determined furnace area, length-width ratio, and requirements for glass melting quality, the thickness and refractory material of the bottom should be reasonably selected, and insulation should be reasonably designed. In addition, bubbling, kiln walls, electric melting assistance, and thermocouple points should be designed according to the actual glass melting situation. The bottom generally uses cast AZS-33WS zircon mullite products.
2.1.2Pool Wall Design
The design of the pool wall is related to the depth of the kiln, which is an important indicator in kiln design and is significantly related to glass quality.
Because glass liquid has poor thermal conductivity and even worse heat penetration, the deeper the furnace, the lower the glass liquid temperature and the poorer the fluidity. Therefore, although the glass liquid near the bottom has a1100~1500temperature, it will not flow, forming a stagnant layer. When the temperature in the furnace changes, the stagnant layer may be carried to the forming section, affecting the glass liquid quality. Based on the above description, the determination of the furnace depth must consider factors such as glass liquid viscosity, melting rate, fuel type, bottom insulation, and the adoption of new technologies (electric melting assistance, bubbling, kiln walls).The upper pool wall/bubbling/kiln wall areas generally use cast AZS-41WS.
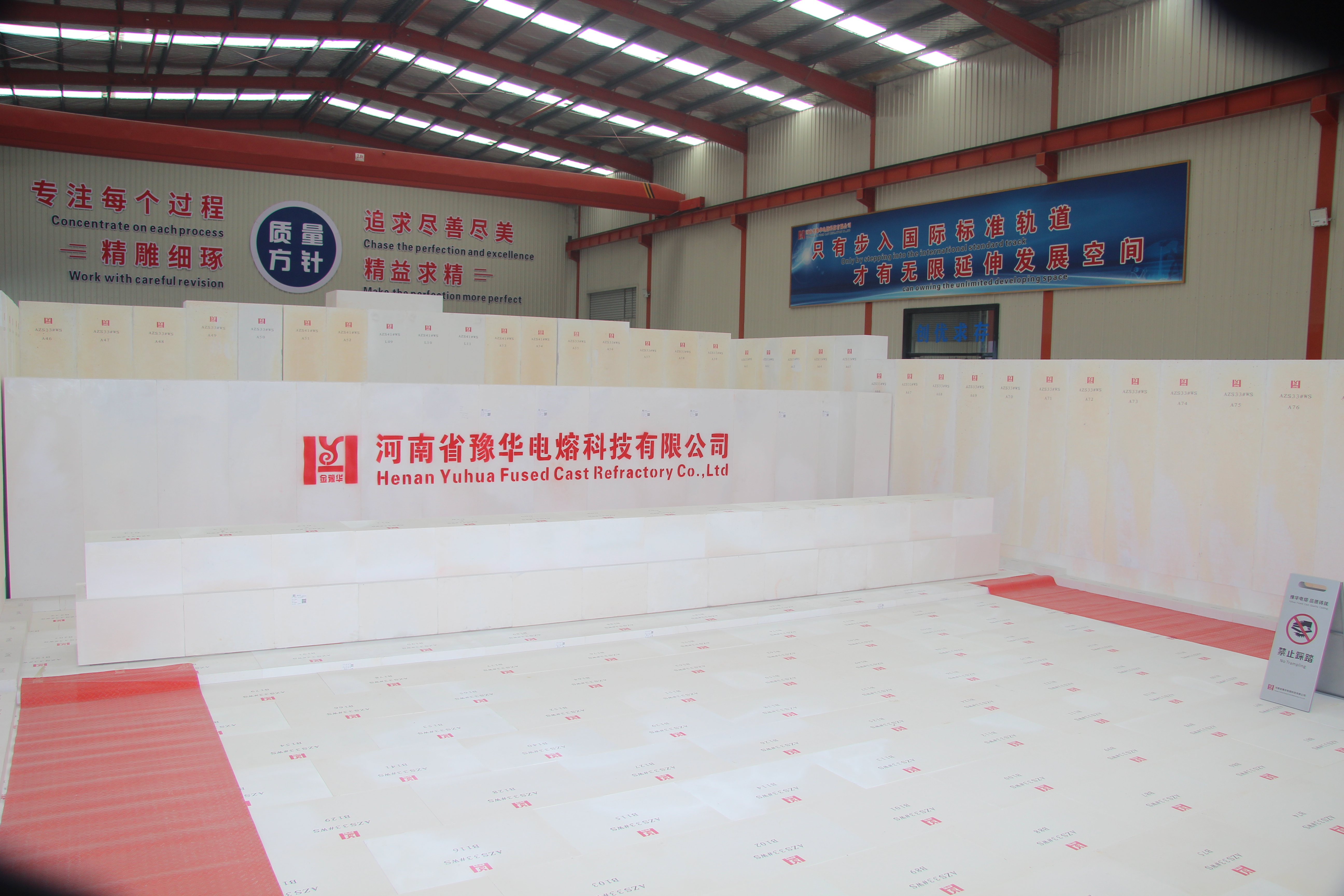
2.1.3Flow Channel
The flow channel is set to allow the clarified glass liquid to cool quickly, block unmelted sand particles and scum on the liquid surface, and regulate the glass liquid flow. The width of the flow channel controls the uniformity of the glass liquid flow; the wider it is, the more uniform it is. The height of the flow channel controls the quality of the glass liquid; the lower it is, the better the quality. The length of the flow channel controls the cooling degree of the glass liquid; the longer it is, the more cooling occurs.
The design of the flow channel is based on the glass liquid flow situation in the flow channel. At the same time, the width, depth, and length of the flow channel can be estimated based on practical experience. The appropriate flow channel form should also be selected based on daily output, product quality requirements, melting and forming temperature, and furnace structural dimensions. Common flow channel forms include flat-bottom, sunken, and inclined types. The flow channel uses cast AZS-41WS zircon mullite products.
2.2Flame Space Design
The flame space consists of a breast wall and a large crown, filled with partially incandescent flame gas supplied from the heat source. Here, the flame gas transfers its heat to the glass liquid, the breast wall, and the large crown. The size of the flame space should allow for complete fuel combustion, ensuring the supply of heat required for melting and clarification, and should minimize heat dissipation to the outside world. The flame space generally uses cast AZS-33WS/PT zircon mullite products.
2.2.1Design of the Large Crown
The large crown has two functions: one is to uniformly distribute radiation along the entire liquid surface, and the other is to act as a reflector of radiant heat. The closer the large crown is to the liquid surface, the more radiant energy is reflected to the glass liquid. From these two points, it can be seen that the design of the large crown requires the crown stock to be as small as possible. At the same time, the height of the large crown must also consider the structural strength of the large crown. The large crown generally uses cast AZS-33WS/PT low-silicon, low-sodium zircon mullite products.
2.2.2Breast Wall Design
After the height of the large crown is determined, the height of the breast wall determines the volume of the flame space. The flame space is not only a space for heat transfer and dissipation, but also a combustion space. The flame space must have a certain volume to ensure complete fuel combustion. The volume of the flame space can be calculated according to the thermal load value of the flame space. Due to the different conditions of each furnace, the thermal load of the flame space cannot use the data of a general combustion chamber; otherwise, the furnace life will be greatly shortened.
Therefore, when determining the height of the breast wall, it is necessary to consider factors such as fuel type, melting rate, melting heat consumption, and furnace scale. The breast wall generally uses cast AZS-33WS/PT zircon mullite products.
3.Selection of Refractory Materials
The selection of refractory materials in all-oxygen kilns is a crucial part, because the composition of the gas after all-oxygen combustion is very different from that of air-assisted kilns, with a significant increase in water and carbon dioxide content, and a sharp increase in alkali vapor concentration. The large amount of water vapor produced by all-oxygen combustion increases the alkali concentration dissolved in the glass liquid, changing the properties of the glass liquid, reducing the viscosity, concentration, and surface tension of the glass liquid, and increasing the crystallization and separation tendency of the glass phase in the glass liquid. At the same time, it makes sodium peroxide and potassium oxide quickly penetrate into the brick. This infiltration process not only changes the glass phase composition of the refractory material but also lowers the glass phase exuding temperature, leading toAZSThe erosion rate of bricks is accelerated. In addition, the alkali vapor in the combustion gas (NaOHandKOH) concentration, upper space temperature, and combustion gas flow pattern have a serious impact on the erosion of silica bricks. Therefore, if a full-oxygen kiln uses silica bricks, to reduce the erosion of silica bricks, it is necessary to maintain a suitable temperature on the surface of the silica bricks, avoid reducing flames to reduce the content of combustion gasNaOH(because reducing flames are conducive to alkali volatilization), and at the same time, it is necessary to reduce the gas flow velocity on the surface of the silica bricks. This is very difficult in terms of kiln operation, operation, and maintenance, so silica bricks are not suitable for use as large bricks in full-oxygen combustion kilns. Some data show that more suitable alternative materials for large bricks are electrofused bricks, including: electrofused zircon-corundum bricks, electrofused zircon bricks, and electrofused corundum bricks.
For the design schemes of other parts of the structure, such as the working pool and the regenerative chamber, the requirements of the glass kiln are not much different, and no detailed explanation will be given. In terms of refractory material selection, since the erosion of refractory materials in full-oxygen kilns is more severe than that in traditional regenerative kilns, the main consideration should be to minimize erosion, improve glass quality, make kiln operation more stable and reliable, effectively increase kiln life, etc., and electrofused zirconia bricks can be considered.
4.Daily operation and maintenance
Excellent masonry quality, reasonable kiln firing and heating operation, only lay a good foundation for the kiln to have a good thermal state and service life. To ensure that the kiln can meet the process requirements for a long time, maximize the service life of the kiln, and daily maintenance work will play a decisive role.
The dangers of kilns come from unknown potential hidden dangers that cannot be dealt with in time and unprepared accidents, and the consequences are often disastrous. Doing a good job of kiln inspection, keeping track of the changes in various parts of the kiln body at any time, and being well-informed, preparing for and preventing possible dangers, this is one of the most fundamental purposes of kiln inspection; secondly, through kiln inspection, the damaged parts and abnormal links of the kiln body can be maintained in time to ensure the normal thermal performance of the kiln, effectively prevent the expansion of problem areas and eliminate the signs of accidents, and provide basic conditions for normal production.
Recommended content
Share to